Behind the scenes at the hidden nuclear robotic works
It would make a great set for a James Bond film.
Vast, futuristic-looking building, check. Lots of men in smart overalls stood at computerised control desks, check. Masses of shiny hi-tech equipment performing mind-bending feats of precision. Check.
But this isn't some underground lair on a remote Caribbean island, it's on an industrial park on the fringes of the Black Country. And this anonymous-looking site is home to one of the biggest players in Britain's nuclear industry.
Thousands of people will drive past Ansaldo Nuclear in Ettingshall, Wolverhampton, without giving a second thought to what goes on behind its gates. But inside the huge yellow building, equipment that would once have been the preserve of sci-fi programmes is made with laser-like precision.
The company produces equipment used in both the nuclear-power and defence industries. And a high percentage of components are manufactured in-house – raw metals come into one end of the building, hand-built, precision equipment comes out of the other.
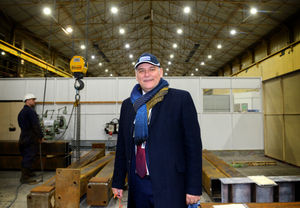
Managing director Andrea Basso speaks with a real excitement as he talks about the products coming out of the factory.
He talks animatedly about the 'moving caves', train-like machines which run on rails above waste silos at plants such as Sellafield in Cumbria, remotely handling radioactive material and safely sealing it under concrete in nuclear-proof containers.
"At a nuclear plant, there is all sorts of waste that has to be disposed of safely," says Mr Basso.
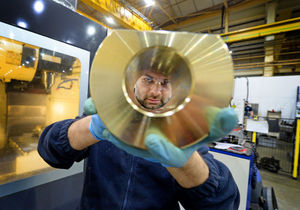
"That can be old overalls, wellington boots, bits of wood, through to fuel rod casings and wrappers they are all dumped in a silo, and just one of those can contain up to nearly 39,000 cubic feet of waste, which the mobile caves can safely recover those nuclear waste from the silos."
Cell leader Pete Andrews demonstrates a robotic arm which replicates the movement of the human hand to deal with radioactive material inside a nuclear-proof container. But while much of the technology is avant-garde, it is good old-fashioned precision which is the real watchword when dealing with nuclear waste.
During our visit, a door which will be used at the European Spallation Source – a world-leading research centre in Sweden – is awaiting inspection.
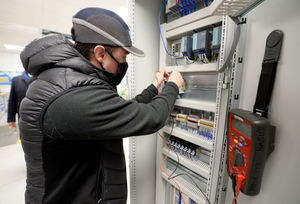
But this is not just a cursory glance, electronic equipment has to be used to ensure there are no flaws in the surface. When you are handling nuclear materials, everything has to be machined, fabricated or assembled to defined quality levels and validated – without the paperwork the manufactured components are useless.
"Everyone is always told how the Challenger space shuttle disaster was the result of a faulty O-ring," says Mr Andrews. "There is no room for any error."
The company recently announced a £12 million deal to develop robot technologies which will be used for the decommissioning of older nuclear power stations, including the Fukushima plant in Japan – which hit the headlines around the world 10 years ago when it was affected by an earthquake – and Sellafield in Cumbria.
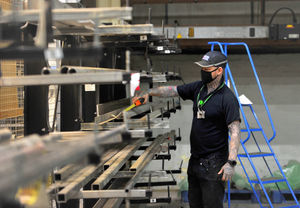
But it is not just nuclear plants coming to the end of their life which make use of the company's equipment. Ansaldo is also working with French energy giant EDF on the new nuclear power plants at Hinkley Point in Somerset.
"With the new power stations, we don't wait until it is time to decommission in 50 years' time, we are thinking about that from the very beginning, from the moment they are designed and built," says Mr Basso.
Looking even further ahead, the company has two teams of engineers in France, working on what could be the first nuclear fusion plant in the world.
The International Thermonuclear Experimental Reactor (Iter) in Provence is a multinational research project, which originated in 1985 as an initiative of post cold-war co-operation between then US president Ronald Reagan, and his Soviet counterpart Mikhail Gorbachev. A total of 35 countries are involved in the scheme, and work on the complex began in 2013.
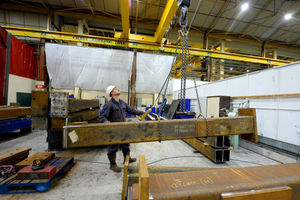
If successful, it could prove to be a game-changer in the way the world sources its electricity.
Mr Basso says: "At the moment, nuclear power comes from nuclear fission, which is about breaking the atom into two, but nuclear fusion is about fusing two atoms together.
"If they can do that, it will produce a long-term source of sustainable energy."
To many, the company is better known as John Thompson's. Founded in 1834 as a boiler maker, the company grew into one of the largest employers in the West Midlands, known the world over for its fuel tankers. It played a crucial role in the Second World War, helping to build the harbour bridges and landing craft used in the D-Day landings. In 1946, it expanded into providing equipment for the emerging atomic energy industry.
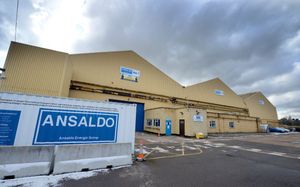
In 1970 it was taken over by Clarke Chapman, which later became the NEI group, and the Wolverhampton plant became known as NEI Thompson. The company was acquired by Rolls-Royce in 1989, and was eventually bought by the Italian Ansaldo Nucleare in 2014.
At the moment the company employs about 450 engineers in the UK with the Wolverhampton plant serving as its head office. Mr Basso says one of the biggest challenges the company faces at the moment is securing skilled workers.
"We are desperately trying to recruit skilled welders, fitters, engineers and quality control personnel," he says.
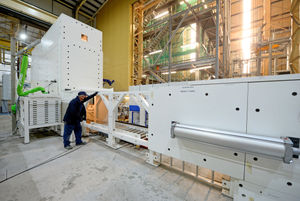
"We are looking for people who are passionate about engineering or manufacturing, who are motivated with a good work ethic, irrespective of where they are in their career."
If nuclear fusion really does become a reality, the opportunities are huge.
Giovanni Verlini, of the International Atomic Energy Agency says it could be the answer to mankind's future energy needs.
"Fuel is inexpensive and abundant in nature, while the amount of long-lived radioactive waste and greenhouse gases produced through fusion are minimal," he says.