VIDEO: Business is suite for Dudley upholsterer's firm
Shaun Hands is working 13 hours a day and, if he's lucky, he gets Sunday afternoons off.
And he's never been happier.
Eighteen months since striking out on his own, the skilled upholster is hand-crafting three piece suites for one of the biggest furniture store companies in the region.
Working with his wife, Lynda, and 19-year-old apprentice Ben Eberle, Shaun says running his own workshop is his dream job.
"This is what I've always wanted; making top quality furniture for people who appreciate it. And people like the fact that it's made here in the Black Country."
His only customer at present is Cousins, the family owned firm of giant furniture stores in Dudley, Tyseley and Manchester. They snap up everything Shaun and the small team at his Black Mills business in Cradley can make.
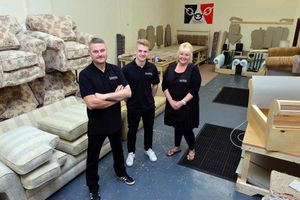
"We can usually produce around 10 suites, of a settee and two armchairs, each week," said Shaun. "At the moment the order period is eight to 10 weeks. We're so busy that I'm trying to find a skilled upholsterer to join us. But it's difficult. There's always been a lot of furniture making in the Dudley area but a lot of it is factory work, where people only learn a part of the process. Here we do everything, so I need someone who can work on every part of the process, from cutting the material and stitching to backing, cording and facing.
"When we started here I was even making the wooden frames, but I've manage to find another firm in Cradley to supply them. A lot of firms use chipboard, plywood or softwoods, but I always use hardwood - beech. That's why I can offer a 10 year guarantee on the frames. It's quality again. What you don't see is as important as what you do see when you are buying a suite. You need firm foundation.
"I design and build my own frames when I and coming up with a new piece, and then my supplier makes them for me."
Including making the frame, Shaun estimates one of his armchairs or settees represent about 10 hours of work.
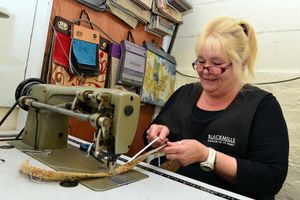
Each piece is a team effort. "The first part is cutting out the pieces of fabric to the patterns, and then sewing them together. Lynda does the sewing for the bodies and we have another girl who sews the cushions. It's the last thing we do at night so we can start straight away next morning.
"Ben will prepared the frame for me and then I start upholstering. I always start with the arms first, then the inside back and the springing, then the platform over the springing. Then its the outside of the body and fancy bits. I usually leave the backs and the legs for Ben to finish off.
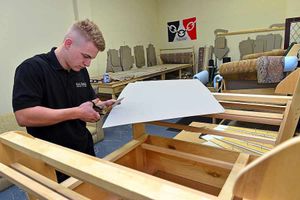
"We always work on one piece at a time, from start to finish. I've tried it where you have several on the go at the same time, but I prefer it this way – it means I can give each piece the attention to detail it deserves."
That attention to detail includes choosing the right kind of foam stuffing, that is durable without being too firm, and the materials for the covers. "You can get Chinese material that is just £3 or £4 a metre, but I get all ours from Belgium – it starts from around £20 a metre but it's just the best stuff. It's got to last, and the Belgian fabric undergoes something like a 150-rub test."
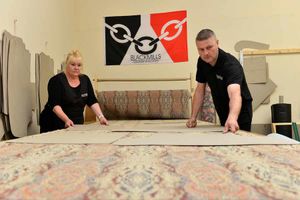
Shaun designs every piece himself: "It starts off as a few ideas in my head, and then some scribbles on paper. I make the cardboard patterns and then I just build it. I'm currently working on one with hydraulics to lift the base for storage – everyone wants more storage space at the moment."
As well as making the suites, Shaun also carries out bespoke work, tweaking settees or chairs for firmness or height to suit individual customers. And the firm also handles re-upholstery work, bringing tired and bedraggled old pieces of furniture back to life.
Now 47, Shaun has been making furniture since he left school. "It was a well paid job at the time and when I started one of the old chaps took me under his wing. I asked him to show me the ropes, and he trained me up over the next six months. He was one of the old craftsmen, who knew the job from start to finish and that is what I wanted to learn.
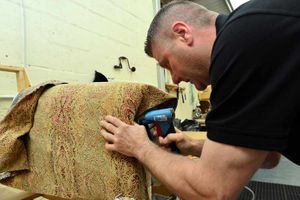
"I've worked in various places over the years, including some of the bigger factories, but this is what I've always wanted: making quality bespoke furniture that will last. I want to make furniture like it used to be, when you knew it would last because it was well made.
"These days there seems to be a lot of demand for that kind of quality. People still want the mass produced stuff, of course, but I think the recession made people think more about quality, about getting something that would last, that was real value for money."
Backed by Lynda, he went solo 18 months ago. She said: "I knew he wasn't happy before. I've had to take on a part-time job so we can make ends meet while we build the business, but we're much happier. The one thing I asked him was that he got someone else to stuff the cushions." She laughs; "Guess what I was doing yesterday?"
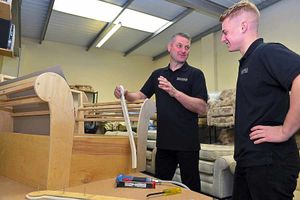
Her hands are reddened from the friction against the hard-wearing fabric. "I used to have lovely nails. Not any more."
The couple, who married in 1986 and have two sons, have worked alongside each other for around 25 years. "I've learned a lot of the skills but there are still things that I have to leave to Shaun."
Just eight weeks ago they were joined by their young apprentice, Ben. A former apprentice player with Aston Villa, he lost his place after suffering an injury and decided he wanted to learn a craft, rather than just get an ordinary job. "I wanted to learn something that would give me a career. It's not like any other kind of job. When you finish a piece of work and you know you've done it well, it's a great feeling. You just step back and look at it and know its good.
"He's a friend of our youngest son," said Lynda. "Shaun wasn't sure it was a good idea but he kept asking so we decided to give me a try.
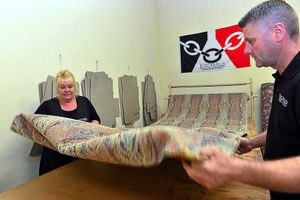
The key to their current success has been the close working relationship with Cousins, particularly with company chairman Robert Shotton and his son John, the managing director.
"I knew they were the sort of store I needed to supply, so I put five sample pieces of furniture in the back of the van and went to see them. I wanted to show them what I could do, and I hoped they might take one of the pieces. They bought all five! And that was that,
"I work very closely with them, making bespoke pieces for clients and talking over designs with them. It's tremendous knowing you've got the family and the sales staff at Cousins behind you.
"They've even said they'll help us get into other stores as we increase production. We couldn't have done this without them."
Shaun is looking for an experienced upholster to join the team at Black Mills. Interested? Then email shaunhands@gmx.com or telephone 01384 568922.