3D printer brings power of creation to Stafford Library
It is the technology used in industry for decades, wielding the power of creation at the touch of a button.

Now, 3D printing has been put into the hands of the public to produce whatever they dream up – and it is easier than you think.
Among the various tablets and touchscreen tables at the new £1 million Stafford Library are two Makerbot Replicators.
Using one of the £2,500 machines we brought our usually flat Express & Star masthead to life in less than one hour.
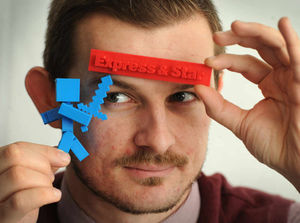
It all starts with an idea. Already there are countless websites on the internet like Thingiverse.com with scores of ready-made designs free to download and are not copyright protected.
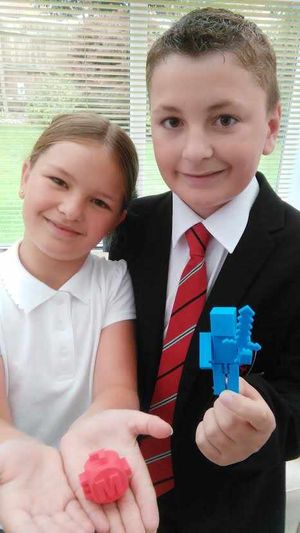
Alternatively you can design your own creation – as we did – using free online software such as Tinkercad.
With remarkable simplicity you can create the design and shape of the item and then save the file – called STL – to load on to the computers at Staffordshire Place.
Here, another programme must be used to determine the size of the design and how detailed it will be.
This is where cost becomes a factor.
But before people think 'ah, here's the catch', the price merely covers the cost of the time and material. It is only £1 per hour of printing time and 20p per gram of material used – which is remarkable value.
Some 3D printing companies which create people's products from their designs charge 10 times the library's rate.
Senior ICT officer Simon Warren said: "The whole idea is to make this technology accessible to the masses and the residents of Staffordshire, as well as to showcase it.
"We want children to do their school projects with it and inspire the engineers of the future. But we also want small businesses who perhaps couldn't afford it before to come in and use it to make something like a prototype."

So how does the machine work? It is loaded up with a coil of bendy plastic-like wire called PLA.
Once the design has been finished and uploaded to the Makerbot using a USB stick, the machine melts the material at a temperature of 215°C (419°F) and forges the item through a needle-thin nozzle one layer at a time.
It is like watching rows of house bricks lay themselves. Ours was a fairly simple design which could be built from the bottom up with little difficulty, but the machine is capable of stunning complexity.
For items with overhanging bits the printer creates a temporary 'raft' out of the PLA for support, which can be snapped off with ease afterwards.
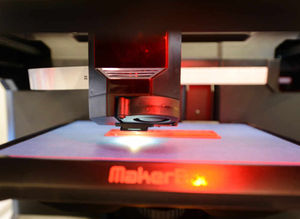
The Makerbot can also build numerous components at one time for the same object using different areas on the 'build plate', which can be fitted together once it is finished. And what of the finished product? Our Express & Star logo was recreated with pinpoint accuracy.
It is also surprising how robust and rigid the once wire-like PLA becomes once it cools – which, by the way, is instant.
But the immediate satisfaction of creating something from scratch is immediately consumed by an overwhelming wonder at what these machines are capable of.
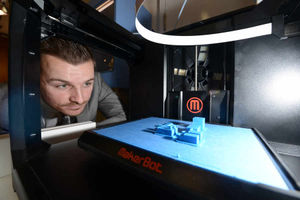
The library already display's around a dozen stunning creations.
Mr Warren said: "From day one the interest in this has been very high. People are just intrigued about it, they have heard about it but have not had the chance to use it until now.
"I must admit I wasn't sure about it. I thought it was a bit of a fad. But having seen what it is capable of I think this is just the start."
At an industrial level, 3D printing is quickly becoming a game-changer in many fields.
Retail giant Amazon is looking into installing 3D printers into its vans for some goods to cut back on storage space and delivery time.
While the technology may well have been around for decades already, in truth it feels like the future.